Spis treści
Czym przeciąć metal?
Cięcie metalu to zadanie wymagające odpowiedniego doboru narzędzi, uzależnionego przede wszystkim od rodzaju obrabianego metalu i jego grubości. Jednym z popularniejszych wyborów jest szlifierka kątowa wyposażona w tarczę przeznaczoną do metalu. Alternatywą są piły do metalu – zarówno te ręczne, pozwalające na większą kontrolę, jak i mechaniczne, umożliwiające szybszą pracę. Piła tarczowa z tarczą widiową również znajduje zastosowanie w wielu sytuacjach. Do precyzyjnych cięć świetnie nadaje się wyrzynarka z odpowiednim brzeszczotem. Z kolei, gdy mamy do czynienia z blachą, idealnym rozwiązaniem są nożyce do metalu. Należy jednak pamiętać, że istnieją specjalistyczne zadania, które wymagają użycia bardziej zaawansowanych metod, takich jak cięcie palnikiem acetylenowo-tlenowym. Coraz częściej spotyka się także cięcie plazmowe i laserowe, a nowoczesną i precyzyjną alternatywą jest cięcie strumieniem wody. Ostateczny wybór metody cięcia powinien uwzględniać kilka kluczowych aspektów:
- pożądaną precyzję,
- grubość obrabianego metalu,
- dostępne zasoby i budżet przeznaczony na ten cel.
Jakie są metody cięcia metalu?
Metody cięcia metalu dzielimy zasadniczo na dwie grupy:
- mechaniczne, oparte na sile fizycznej,
- termiczne, wykorzystujące ciepło.
Do pierwszej kategorii zaliczamy cięcie:
- piłą,
- nożycami do blachy,
- a także różnego rodzaju obróbkę plastyczną, jak choćby cięcie nożowe czy rozdzielanie materiału przez przebijanie otworów.
W tej grupie znajdziemy również techniki wykorzystujące jedną lub dwie krawędzie tnące, a gilotyny hydrauliczne są jej reprezentatywnym przykładem. Z kolei w metodach termicznych kluczową rolę odgrywa temperatura, realizowana za pomocą:
- palnika acetylenowo-tlenowego,
- plazmy,
- lasera.
Istnieje także alternatywna technika, cięcie strumieniem wody, precyzyjnie zwane cięciem wodnym. Decyzja o wyborze konkretnej metody powinna uwzględniać kilka istotnych aspektów: rodzaj obrabianego metalu, jego grubość oraz pożądaną dokładność finalnego elementu. Należy pamiętać, że każda z omawianych technik ma swoje atuty i ograniczenia, które należy brać pod uwagę.
Jakie parametry powinny być brane pod uwagę przy cięciu metalu?
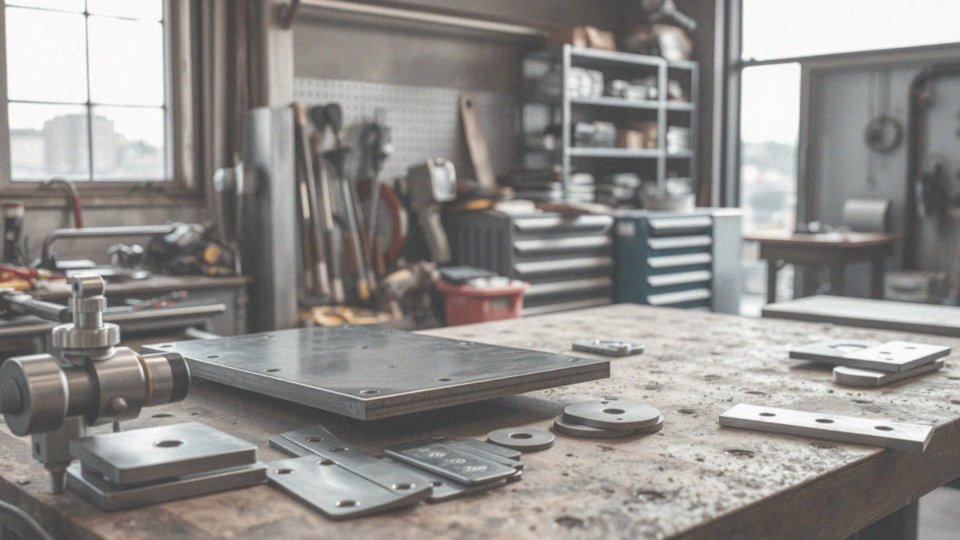
Podczas obróbki metali kluczowe znaczenie mają trzy aspekty:
- materiał,
- jego grubość,
- wymagana dokładność cięcia.
To one determinują wybór odpowiedniej techniki i narzędzia. Przykładowo, stal nierdzewną tniemy inaczej niż aluminium czy miedź, które wymagają odmiennych podejść. Grubość obrabianego elementu bezpośrednio wpływa na potrzebną moc urządzenia. Natomiast w przypadku precyzyjnych projektów, cięcie laserowe często okazuje się niezastąpione. Długość samej linii cięcia również ma znaczenie – do długich, prostych odcinków lepiej sprawdzą się metody mechaniczne. Odpowiedni dobór narzędzia ma decydujący wpływ na efektywność i jakość wykonania. Pamiętajmy także o chłodzeniu, które zapobiega przegrzewaniu się zarówno metalu, jak i samego narzędzia, szczególnie istotne przy obróbce termicznej. Nie zapominajmy o priorytecie, jakim jest bezpieczeństwo – stosujmy zawsze odpowiednie środki ochrony osobistej. Warto mieć na uwadze, że zwłaszcza cięcie termiczne, może wpływać na mikrostrukturę metalu, szczególnie w przypadku stali.
Jakie są kluczowe aspekty doboru narzędzi do cięcia metalu?
Wybór odpowiedniej metody cięcia metalu w dużej mierze zależy od jego rodzaju. Twardość, specyficzny skład chemiczny oraz grubość metalu – to czynniki, które determinują zarówno technikę cięcia, jak i narzędzie, którego użyjemy. Przykładowo, do obróbki twardych stopów metali niezbędne są tarcze diamentowe, podczas gdy do cięcia miękkich metali wystarczy pospolity brzeszczot. Grubość obrabianego elementu ma niebagatelny wpływ na wymaganą moc narzędzia. Im grubszy materiał, tym solidniejsze narzędzie jest potrzebne, a w niektórych przypadkach konieczne może być użycie przecinarki plazmowej. Istotna jest również precyzja cięcia, szczególnie gdy zależy nam na dokładnych detalach – wtedy idealne okazują się metody takie jak cięcie laserowe lub strumieniem wodnym, gwarantujące wysoką dokładność. Nie można zapomnieć o ergonomii narzędzia oraz o bezpieczeństwie pracy, które nabiera szczególnego znaczenia podczas długotrwałego użytkowania. Dodatkowo, rodzaj cięcia – proste, krzywoliniowe czy pod kątem – bezpośrednio wpływa na wybór narzędzia. Na przykład, wyrzynarka świetnie sprawdzi się przy cięciach po łuku. Należy również rozważyć, czy po cięciu planowana jest obróbka termiczna. To, czy praca wykonywana jest w domowym zaciszu, czy w profesjonalnym warsztacie, ma duże znaczenie. W warunkach domowych szlifierka kątowa może okazać się wystarczająca, jednak profesjonalne warsztaty wymagają zazwyczaj specjalistycznych maszyn do obróbki metalu. Nie bez znaczenia są też koszty eksploatacji, które należy wziąć pod uwagę, dobierając narzędzie.
Jakie narzędzia są najważniejsze do cięcia metalu w warsztacie?
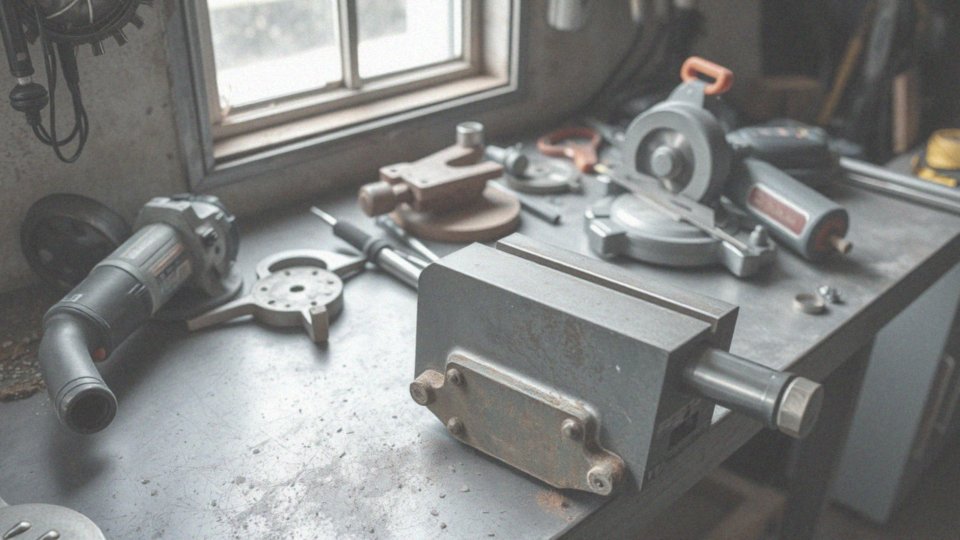
W każdym warsztacie, kluczowe są narzędzia przeznaczone do obróbki metalu, zapewniające precyzję i efektywność. Ale, które z nich zasługują na miano najważniejszych?
- Szlifierka kątowa to niezwykle uniwersalne urządzenie, którego możliwości rozszerza wymienna tarcza. Dzięki temu znakomicie radzi sobie z różnymi metalami, od stali po aluminium, a także umożliwia szlifowanie i polerowanie,
- do wyboru mamy piły ręczne i mechaniczne. Te pierwsze pozwalają na wyjątkowo precyzyjne cięcia, z kolei piły mechaniczne znacząco przyspieszają realizację większych projektów,
- piła tarczowa z tarczami widiowymi to idealne rozwiązanie do cięcia rur i profili metalowych. Same tarcze widiowe charakteryzują się dużą trwałością i zapewniają dokładne cięcie, co czyni ją bardzo wydajnym narzędziem,
- wyrzynarka z odpowiednio dobranym brzeszczotem do metalu pozwala na wycinanie nawet najbardziej skomplikowanych kształtów w arkuszach blachy. Należy pamiętać o odpowiednim doborze brzeszczotu, dopasowując go do grubości i twardości obrabianego materiału,
- nożyce do metalu, zarówno ręczne, jak i elektryczne, okazują się niezastąpione przy cięciu blach. Wersje elektryczne podnoszą komfort pracy, szczególnie podczas obróbki dużych powierzchni.
Oprócz wyżej wymienionych, nie można zapomnieć o narzędziach pomocniczych.
- Imadło, stabilnie mocując element obrabiany, bezpośrednio przekłada się na bezpieczeństwo i precyzję cięcia,
- stół warsztatowy tworzy stabilną bazę do pracy, umożliwiając bezpieczne wykonywanie zadań,
- pilniki i papier ścierny służą do wygładzania krawędzi po cięciu, usuwając wszelkie zadziory i wyrównując powierzchnie,
- natomiast miarki i znaczniki umożliwiają precyzyjne odmierzanie i oznaczanie materiału przed cięciem, co jest kluczowe dla zachowania dokładności wymiarów.
Jakie narzędzia powinienem używać do cięcia elementów stalowych?
Do cięcia elementów stalowych, takich jak rury, blachy czy pręty, możemy wykorzystać różnorodne narzędzia. Wybór odpowiedniego narzędzia powinien uwzględniać grubość i kształt ciętego elementu, a także oczekiwaną precyzję wykonania. Popularne opcje to:
- szlifierka kątowa wyposażona w tarczę przeznaczoną do cięcia stali – jest uniwersalna i łatwa w transporcie,
- piła do metalu, która może być ręczna, zapewniająca większą kontrolę nad cięciem, lub mechaniczna, znacznie przyspieszająca pracę,
- piła tarczowa z tarczą widiową, która efektywnie radzi sobie z cięciem rur i profili, szczególnie przy bardziej wymagających zadaniach,
- wyrzynarka z odpowiednim brzeszczotem do metalu, idealna do precyzyjnego cięcia cienkich blach,
- nożyce do blachy, dostępne w wersji ręcznej lub elektrycznej, niezastąpione do cięcia cienkich arkuszy stali,
- palnik acetylenowo-tlenowy, do cięcia bardzo grubych elementów stalowych, choć jego obsługa wymaga wprawy i doświadczenia.
Jak wybrać odpowiednie ostrza do cięcia stali nierdzewnej?
Odpowiedni dobór ostrzy do cięcia stali nierdzewnej ma fundamentalne znaczenie dla precyzji i trwałości obróbki. Zatem, jak wybrać właściwe narzędzie? Optymalne rezultaty osiągniesz, sięgając po ostrza wykonane ze stali szybkotnącej (HSS), a szczególnie polecane są te z dodatkiem kobaltu (HSS-Co), który podnosi ich twardość i odporność na wysokie temperatury, co jest nieocenione przy pracy ze stalą nierdzewną. Alternatywnie, ostrza z węglika spiekanego to solidny wybór, charakteryzujący się dużą wytrzymałością i odpornością na ścieranie, co przekłada się na ich dłuższą żywotność. Warto również rozważyć tarcze diamentowe lub ceramiczne, jeśli specyfika pracy tego wymaga. Decydując się na tarczę do szlifierki kątowej, zwróć uwagę na oznaczenia wskazujące na jej przeznaczenie do stali nierdzewnej – to zapewni kompatybilność z tym materiałem. W trakcie pracy monitoruj parametry cięcia, aby uniknąć przegrzania stali. Ostrza o mniejszej grubości generują mniej ciepła, co skutkuje czystszym cięciem, podczas gdy te grubsze oferują większą trwałość przy obróbce większych elementów. Nie bez znaczenia jest także rozmiar zębów lub ziarna ściernego: drobniejsze zęby doskonale sprawdzą się przy precyzyjnych cięciach, a większe umożliwią szybsze usuwanie materiału.
Co to jest cięcie gazowe i jakie ma zastosowania?
Cięcie gazowe, powszechnie stosowane w obróbce metali, wykorzystuje płomień gazowy, zwykle tlenowo-acetylenowy lub tlenowo-propanowy. Proces ten rozpoczyna się od nagrzania metalu do temperatury zapłonu, po czym strumień tlenu usuwa stopiony materiał. Metoda ta doskonale sprawdza się w przypadku stali niskowęglowej, radząc sobie nawet z grubymi elementami. Z drugiej strony, nie jest zalecana do obróbki stali nierdzewnej, aluminium oraz innych metali nieżelaznych. Stalowe elementy uzyskane w procesie cięcia gazowego znajdują szerokie zastosowanie w:
- konstrukcjach stalowych,
- budownictwie,
- przemyśle stoczniowym.
Warto jednak podkreślić, że technika ta jest najbardziej efektywna tam, gdzie precyzja cięcia nie odgrywa pierwszorzędnej roli.
Co to jest cięcie plazmowe i kiedy jest używane?
Cięcie plazmowe to zaawansowana metoda obróbki metali, wykorzystująca strumień plazmy o ekstremalnie wysokiej temperaturze. Ten zjonizowany gaz błyskawicznie przetapia i wydmuchuje materiał w miejscu cięcia, umożliwiając precyzyjne oddzielanie metali przewodzących prąd elektryczny. Wszechstronność i efektywność plazmy sprawiają, że jest ona niezastąpiona w rozmaitych sektorach przemysłu. W produkcji, na przykład, wykorzystuje się ją do precyzyjnego cięcia blach, rur, profili stalowych (w tym nierdzewnych) oraz aluminium. Warsztaty samochodowe cenią ją za możliwość szybkiej naprawy karoserii poprzez wycinanie skorodowanych fragmentów i wprowadzanie modyfikacji. W budownictwie, cięcie plazmowe ułatwia przygotowanie elementów do spawania, umożliwiając precyzyjne wycinanie otworów i nadawanie kształtów różnym materiałom. Pasjonaci hobby i rzemiosła artystycznego doceniają jej potencjał w tworzeniu oryginalnych dekoracji i rzeźb. Nawet metaloplastyka korzysta z zalet tej technologii.
Lista atutów cięcia plazmowego jest długa. Możemy wymienić:
- imponującą prędkość cięcia, szczególnie ważną przy obróbce cienkich blach,
- możliwość pracy z szerokim spektrum metali, w tym ze stalą, aluminium, miedzią oraz ich stopami,
- minimalną strefę wpływu ciepła, ograniczającą ryzyko deformacji materiału,
- brak konieczności wstępnego podgrzewania obrabianego elementu, w odróżnieniu od cięcia gazowego,
- możliwość automatyzacji procesu za pomocą systemów CNC, co znacząco zwiększa precyzję i wydajność.
Podsumowując, cięcie plazmowe zyskuje przewagę nad innymi metodami dzięki swojej precyzji, szybkości i uniwersalności w obróbce różnorodnych metali. Często bywa jedynym realnym rozwiązaniem tam, gdzie tradycyjne metody cięcia, jak cięcie gazowe, okazują się niewystarczające lub wręcz niemożliwe do zastosowania.
Czym jest cięcie wodne i kiedy się je stosuje?
Cięcie wodą, inaczej nazywane hydro-abrasive cutting (HAC), to technika precyzyjnego rozdzielania materiałów. Wykorzystuje ona strumień wody pod ekstremalnie wysokim ciśnieniem, często wzbogacony o dodatek ścierny, taki jak elektrokorund. To umożliwia obróbkę nawet bardzo twardych substancji.
Kiedy warto sięgnąć po tę technologię? Zwłaszcza wtedy, gdy kluczowa jest wysoka precyzja, tak jak w przemyśle lotniczym, gdzie idealne wymiary są niezbędne. Co więcej, cięcie wodą doskonale sprawdza się w przypadku materiałów wrażliwych na wysokie temperatury, np. niektórych kompozytów. Technologia ta ma wszechstronne zastosowanie – pozwala na obróbkę metali, kamienia, szkła i tworzyw sztucznych. Istotną zaletą jest fakt, że nie wpływa na strukturę materiału w miejscu cięcia. Jest to szczególnie ważne w branżach takich jak przemysł spożywczy, przy obróbce stali nierdzewnej.
Cięcie wodą umożliwia pracę z elementami o znacznej grubości, jednocześnie minimalizując straty materiału. Jest to istotne w jubilerstwie oraz wszędzie tam, gdzie efektywne wykorzystanie surowców ma kluczowe znaczenie. Dodatkowo, proces cięcia jest czysty i ekologiczny, ponieważ nie generuje szkodliwych oparów ani pyłów. Pozwala na precyzyjne formowanie materiałów o zróżnicowanych, nawet nieregularnych kształtach oraz umożliwia nacinanie materiałów warstwowych.
Co to jest cięcie laserowe i jakie ma zalety?
Cięcie laserowe to zaawansowana technologia, w której skoncentrowana wiązka światła topi lub odparowuje metal, pozwalając na uzyskanie niezwykle dokładnych krawędzi. Ta metoda charakteryzuje się wysoką precyzją obróbki oraz minimalną strefą wpływu ciepła (HAZ), co przekłada się na mniejsze ryzyko odkształceń materiału. Co więcej, cięcie laserowe umożliwia wycinanie nawet najbardziej złożonych kształtów z zachowaniem pełnej powtarzalności, co czyni je idealnym rozwiązaniem dla produkcji seryjnej.
Jakie konkretne korzyści płyną z zastosowania tej technologii?
- laser gwarantuje wyjątkową precyzję cięcia, co jest nieocenione przy wytwarzaniu elementów wymagających absolutnej dokładności,
- strefa wpływu ciepła jest minimalna, co zapobiega zmianom w strukturze metalu i potencjalnym deformacjom,
- uniwersalność lasera pozwala na obróbkę różnorodnych metali, w tym stali, aluminium i miedzi,
- umożliwia również tworzenie skomplikowanych wzorów, trudnych do uzyskania innymi metodami,
- powtarzalność procesu zapewnia identyczne rezultaty w produkcji seryjnej,
- brak kontaktu mechanicznego eliminuje zużycie narzędzi i ryzyko uszkodzenia obrabianego materiału.
Dzięki swoim zaletom, cięcie laserowe znalazło szerokie zastosowanie w wielu gałęziach przemysłu, takich jak motoryzacja, lotnictwo, elektronika oraz medycyna. Jest nieodzowne wszędzie tam, gdzie kluczową rolę odgrywa precyzja wykonania, a dokładność i estetyka są priorytetem przy produkcji metalowych części.
Jakie są różnice w cięciu różnych metali, takich jak stal i aluminium?
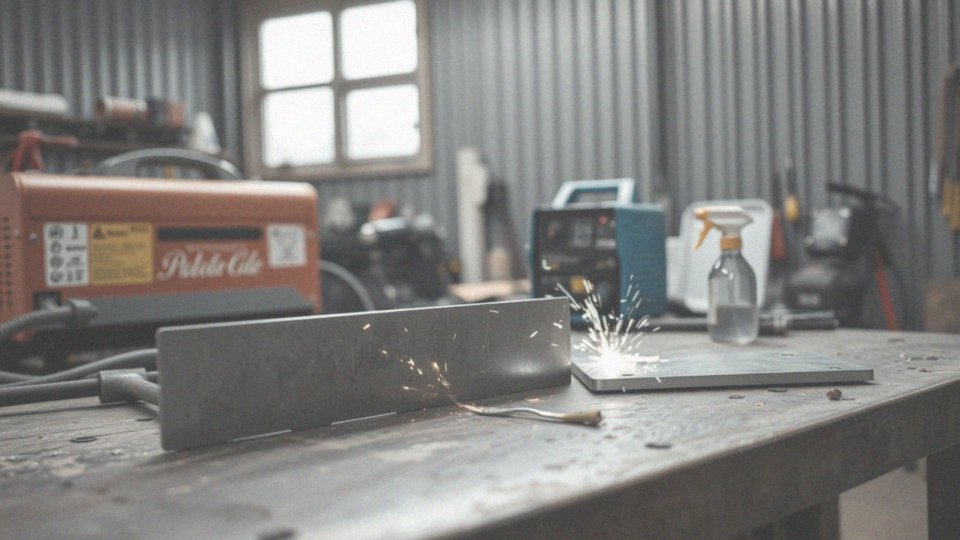
Różnice w procesie cięcia stali i aluminium wynikają z ich odmiennych właściwości. Stal, jako materiał twardszy i o wyższej temperaturze topnienia niż aluminium, wymaga zastosowania specyficznych metod obróbki. Do cięcia stali powszechnie używa się szlifierek kątowych wyposażonych w odpowiednie tarcze, a alternatywnie, w niektórych przypadkach, wykorzystuje się piły tarczowe. Natomiast grube elementy stalowe najczęściej przecina się metodą gazową.
Aluminium, ze względu na swoją niższą temperaturę topnienia i większą plastyczność, jest bardziej podatne na odkształcenia pod wpływem ciepła. Z tego powodu, w przypadku cięcia aluminium, zaleca się stosowanie technik minimalizujących wpływ termiczny. Idealnie sprawdzą się tutaj:
- cięcie plazmowe,
- cięcie laserowe,
- cięcie wodne.
Można również sięgnąć po specjalistyczne tarcze widiowe oraz brzeszczoty przeznaczone do obróbki metali miękkich. Podczas pracy z aluminium niezwykle istotne jest precyzyjne ustawienie parametrów cięcia, w szczególności kontrola prędkości posuwu oraz skuteczne chłodzenie. Takie działania pozwalają uniknąć przegrzania i deformacji materiału, a także zminimalizować ryzyko powstawania nieestetycznych zadziorów.
Ostateczny wybór metody cięcia jest podyktowany grubością materiału, wymaganą precyzją oraz dostępnością odpowiednich narzędzi. Cięcie laserowe zapewnia najwyższą dokładność, natomiast cięcie strumieniem wodnym pozwala zachować niezmienioną strukturę materiału, co w niektórych zastosowaniach jest kluczowe.